Share
Pin
Tweet
Send
Share
Send
De taak was bovendien om een kas van 3 meter breed, 8 meter lang te krijgen, met de mogelijkheid om een persoon van gemiddelde lengte vrij te verplaatsen, d.w.z. tot 1,8 meter. Daarom besloot ik om een polycarbonaat kas te maken met een frame gemaakt van een metalen profiel van mijn eigen ontwerp.
Het frame geschetst voornamelijk uit een lichtmetalen buis en hoek. Het ontwerp van het "dak" maakte het noktype, de gebruikelijke gevel, getest op betrouwbaarheid. De hoogte van de nok varieert afhankelijk van de weersomstandigheden in uw omgeving, ik heb gekozen met een spanthoek van 45 graden, zodat sneeuw in de winter gemakkelijk kan glijden. Bij het installeren van de spanten versterkt met een dwarsbalk, verbinden met een driehoek.
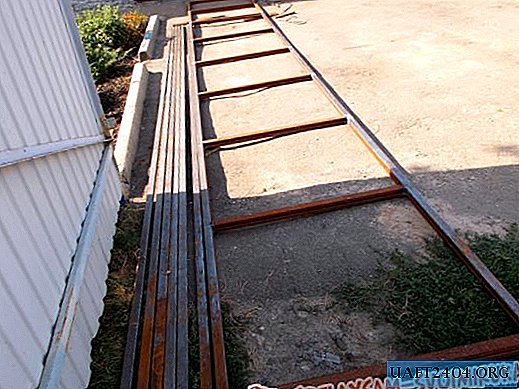

Standaard polycarbonaatplaten hebben de volgende afmetingen: dikte 4 mm, breedte 2,1, lengte 6 meter. Ik vestig de aandacht op de kwaliteit van polycarbonaat, ik gebruikte de Russische fabrikant Sunnex, laten we zeggen dat het van gemiddelde kwaliteit is, er is een duurzamer en dichter materiaal, dit is merkbaar in de doorbuiging, structuur en gewicht, doorvoer naar ultraviolet. De keuze is aan u, maar niet opslaan, om de doorbraak onder belasting van sneeuw of wind te voorkomen.

Traditioneel begon de bouw met het leggen van een kleine fundering, omdat in mijn geval de kas grondig moest worden bevestigd en om vervormingen te voorkomen. Ik heb dunne funderingsblokken en dwarsliggers van gewapend beton aangebracht. Bouten voor krachtige bevestigingen van het frame rond de hele omtrek van de kas werden in de "normale" gaten van de dwarsliggers gelegd. Tijdens de installatie van de gehele in delen gelaste frameconstructie dienden deze bevestigingsmiddelen als een bevestigingsservice voor de verdere installatie van het bovenste rooster (op dit moment waren echter assistenten nodig om het frame te ondersteunen).
Caraca's gemaakt van een metalen profielpijp 20 * 40 mm met een grill tot 1 meter, anders kan polycarbonaat in de winter door ijzige sneeuw vallen. Hij maakte de onderste uiteinden van de hoek 35 * 35 mm zodat de deur bij de voeg zou sluiten.
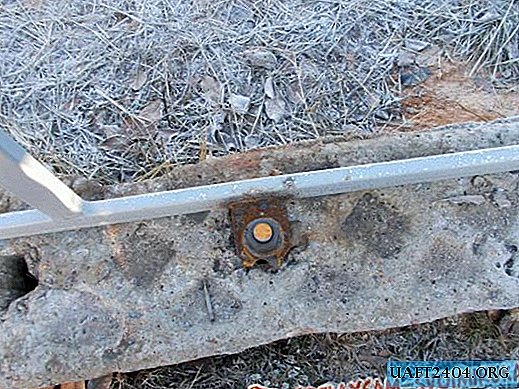
Geen onbelangrijk moment, we ontwerpen het frame zodanig dat polycarbonaat het meest economisch wordt gesneden, namelijk dat we de zijwanden 1,05 meter hoog maken, waarbij we rekening houden met het in de lengte doormidden snijden. Rafters 2,1 meter lang, om twee vellen op het dak te bevestigen en een extra vel in stukken van 2 meter te snijden.
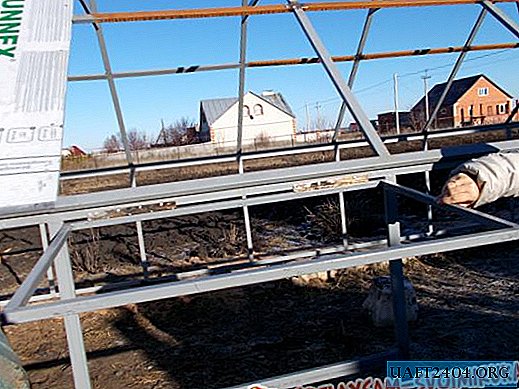
Naast de deur zorgde ik voor twee vensters voor ventilatie in de kas, vanaf de lijzijde aan het einde en de zijkant van de structuur, 20 * 20 mm gelast uit een licht profiel. Ik heb de ramen op de pianoscharnieren geïnstalleerd, ze zijn vrij dun en interfereren niet met het polycarbonaat zodat het goed in het frame past.

Alle verbindingen en gaten in het polycarbonaat gingen door siliconen en vanaf de onderkant van de opening met montageschuim. Het frame op de plaatsen van lassen werd geschuurd, geverfd met een corrosiewerende verbinding en verf.
Materiaal voor het bouwen van een kas:
- polycarbonaat 2,1 * 6 m. - 5 platen;
- metalen profielbuis 20 * 40 mm - 120 meter;
- metalen profielbuis 20 * 20 mm - 18 meter;
- zelftappende schroeven met een sluitring en een boor - 1000 stuks;
- funderingsblokken (dwarsliggers) met een totale lengte van 22 meter;
- zand voor het leggen van de fundering;
- bevestigingsmiddelen en bouten voor het frame;
- corrosiewerende verf;
- scharnieren van deuren en piano's, deurknoppen;
- laselektroden 3 kg.
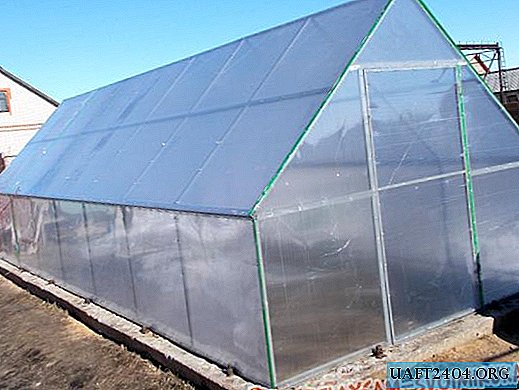
Voordelen van de kas: solide gevelgevel; stijve bevestiging van het frame; vereiste geometrische afmetingen; gebruiksgemak; de mogelijkheid om materiaal zuinig te snijden; weinig gewrichten.
Nadelen: de kruising van het dak en de zijspanten bleek als het ware versterkt te zijn met twee profielen, wat economisch niet haalbaar is.
Share
Pin
Tweet
Send
Share
Send